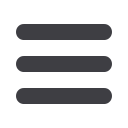

EuroWire – July 2009
56
Wire products for the automotive industry
Flexible flat cables
Flexible flat cables (FFC) have found widespread use in the automotive industry. Compared to traditional cabling and automotive
wiring harness, using flat conductor technology solutions in particular save space, weight and costs.
As a leader in coating equipment for optical fibres, Medek & Schoerner has
developed a new pressureless cold process for the production of FFCs using
UV cured resins, thus ensuring the perfect geometrical accuracy of the cable
at high production speeds. The same procedure can also be employed in-line
with an extruder to position the individual flat cables accurately as they enter
the extruder head.
Lamination and extrusion have been the processes most commonly used
for the production of FFCs today. The disadvantage of lamination is its
extremely low production speed. Extrusion is unsuitable for the production
of micro FFCs due to the high temperatures and pressures encountered in
the extruder head: these make it impossible to maintain accurate geometrical
dimensions and precise positioning.
Hybrid FFC structures such as copper and optical fibre combinations
and other materials can be employed more or less as a standard with
the new FFC production process.
When marking automotive wires the outer sheathing and insulation of
wires is generally identified by printing them with text information or by
coding with coloured rings. For such applications Medek & Schoerner
offers high quality gravure printers for text printing at speeds up to
1,200m/min, and ring markers for speeds up to 2,500m/min.
Medek & Schoerner GmbH – Austria
Fax
: +43 1 982 72 96
:
m+s@medek.atWebsite
:
www.medek.atHybrid, electrical and fuel cell propulsion systems require harnesses that
make special demands on HV cables and conductors. Leoni’s Hivocar
®
range offers cables for different temperature ranges. Especially developed
for 150°C requirements, Hivocar 150 is designed for excellent thermal
properties, beyond ISO 6722 and SAE J2183 standard as well as the LV 212
standard-specified temperature class D ( of –40 to +150 °C).
With respect to long-term ageing, short-term ageing and thermal
overload this new cable exceeds the required standards. Internal test
results show that a Leoni Hivocar 150 cable can be used at the upper
temperature limit for as long as 4,000 hours. This is in contrast to a
standard 150°C cable, typically designed to withstand this temperature
for 3,000 hours. Based on the choice of materials, irradiated cross-linked
PE insulation in combination with a TPE-U sheath, Hivocar 150 cables
are believed to be significantly more robust in regards to both thermal
and mechanical characteristics.
Leoni Hivocar products are also available as silicone types to meet
long-term temperature requirements of up to 200°C. Hivocar 200 offers
a high performance similar to ISO 6722 requirements.
Excellent bending performance at lower temperatures and resistance
against environmental influences will qualify these types for several HV
applications in the automotive segment.
In addition, all Leoni cables are optimised for superior EMI/EMC
performance as well as flexibility. Leoni Hivocar exceeds the special
requirements for all hybrid and fuel cell power trains.
Leoni AG – Germany
Fax
: +49 911 2023 231
:
info@leoni.comWebsite
:
www.leoni.comHivocar
®
for high temperatures
▲
▲
Leoni’s Hivocar 150 and 200 for automotive
applications
▲
▲
Flat, flexible cable for automotive applications
▼
▼
Ring marking on an automotive cable