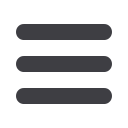

EuroWire – July 2009
57
Wire products for the automotive industry
Flat and shaped wire
The Seneca Wire Group, consisting of Seneca Wire & Manufacturing Company and FĒNIX, LLC is one of the oldest wire manufacturers
in North America, founded in 1905 in Fostoria, Ohio, USA. The Seneca Wire Group’s technologies, experience and expertise in the
production of round, flat, and shaped tempered wire products support leading market positions in the company’s target markets.
FĒNIX, LLC, established in 2005 in Wapakoneta, Ohio, USA, is the company’s production facility for round and shaped tempered wire
in a diameter range of 5mm to 17.5mm, utilising modern cold drawing and induction tempering technologies.
The Seneca Wire & Manufacturing Company specialises in the production of flat and shaped tempered wire in a range of 2mm to
6mm thicknesses, 4.75mm to 16mm widths and round tempered wire in 2mm to 5mm diameters. Wire products are produced
by Seneca Wire and FĒNIX, LLC in high carbon grades SAE 1050-1086 and micro-alloyed grades including SAE 9254, certified to
a wide number of ASTM, DIN, BS and JIS specifications. End use markets served by the Seneca Wire Group include automotive,
construction, agricultural, mining and quarrying, truck safety brakes, and suspension spring markets.
The SenecaWire Group – USA Fax
: +1 419 435 9265
:
info@senecawire.comWebsite
:
www.senecawire.comAluminium automotive wire drawing
and bunching technology
In order to save weight, leading car manufacturers are planning on replacing copper conductors, of 6mm
2
to 50mm² cross section,
with aluminium conductors. The production equipment for aluminium wires – drawing lines, payoffs and bunching machines – must
meet added and more difficult demands. Maschinenfabrik Niehoff has recently developed new aluminium multi-wire drawing and
annealing technology.
Experience of the MH 120 type 2-wire intermediate drawing line with integrated RA 200 annealer, developed for drawing of up to
30 different aluminium alloys wires, has helped the design of the MMH 104/RMA 201 type multiwire drawing and annealing line.
The line is designed for the simultaneous drawing of eight or
sixteen aluminium or aluminium alloy wires from a maximum
inlet diameter of 2.5mm to a finish diameter of 0.15 to 0.6mm
with inline annealing and can work with a maximum speed of
31.5 m/s. The wires have highly homogeneous characteristics to
meet the strictest specifications and processing requirements.
The MMH 104 drawing machine can be used with different
drawing lubricant supply systems and operated with drawing
oil or drawing emulsion for a clean operation. Further features
include special die holders and built-in drawing capstan sprayers
tailor-made for the specific requirements of aluminium wire
drawing and a vacuum system for extracting oil mist from the
drawing area and returning it to the drawing lube system.
The RMA 201 continuous resistance annealer is designed for
aluminium and aluminium alloy wires. The two-zone annealing
principle with short annealing sections, promotes economical
and ecological energy consumption. The entire wire section from the final die in the MMH 104 to the end of the annealing operation
is fully sealed off from the outside. In order to avoid oxidation of the aluminium wire surface nitrogen is used as protective
atmosphere.
Niehoff’s D series double twist bunching machines are suitable for the
bunching of aluminium and aluminium alloy wires. The one-bow design
results in a significantly reduced energy consumption and noise emission
compared to conventional bunching machines. D-series machines can
be equipped with bows whose geometries and coatings are specially
adapted to the requirements of aluminium wires. By means of a load cell
inside the cradle, the wire tension on the spool is infinitely adjustable,
monitored and controlled within tight tolerances across the entire bobbin
filling. As an option, the bunchers can be equipped with the NBAT (Niehoff
bunching automatic traverse) device that automatically detects spool
flanges and controls the traverse width of empty and full spools by means
of optoelectronic sensors. As the spools are filled perfectly, the strands can
be paid off tangle-free and without wire damages even at very high speeds.
Maschinenfabrik Niehoff GmbH & Co KG – Germany
Fax
: +49 9122 977 155
:
info@niehoff.deWebsite
:
www.niehoff.de▲
▲
A detail from the D 631 type series double twist bunching machine
equipped for aluminium and aluminium alloy wires
▲
▲
A detail from the MMH 104/RMA 201 multiwire line