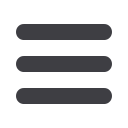

EuroWire – July 2009
61
technical article
K3120-10 is a comparable sample with
a low viscosity, but it differs from the
K2500-10 by exhibiting a non-Newtonian
response at low shear rates. It would be
inferred that this rheological characteristic
would delay relaxation of molecular orien-
tation after completion of the drawing
operation resulting in higher shrink-
back. This has been confirmed through
subsequent shrinkback experiments.
To further understand the relationship
between PVDF structure and shrinkback,
stress
relaxation
experiments
were
performed. It can be reasoned that a
polymer having the ability to relieve
stresses quickly in the melt state will
exhibit lower polymer orientation and
consequently lower shrinkback. The stress
relaxation experiments were conducted
using the ARES-LS strain rheometer
using 25mm parallel plate geometry. A
step strain of 100% was applied to PVDF
samples and the decay of modulus was
recorded as a function of time. Results of
these experiments can be seen in
Figure 2
.
As expected, the higher viscosity samples
such as K2750-01 and K3120-50 show
a relatively slow relaxation response
whereas the lower viscosity samples such
as K2500-10 and K3120-10 exhibit a fast
relaxation response. The quick relaxation
response for these low viscosity samples
should result in less polymer alignment in
the final product.
For the purposes of this paper, the
relaxation times for each PVDF sample to
reach the arbitrary value of 100 Pa were
examined. These values can be observed
in
Table 2
.
As can be seen in
Table 2
, the relaxation
response for the K2500-10 is considerably
faster than any of the other products
tested. A significant amount of this
behaviour can be attributed to the
structure of this product. When comparing
K2500-10 to K3120-10, it is noted that
the relaxation response for the K2500-10
(random copolymer distribution) is signi-
ficantly faster than for the K3120-10
(non-random copolymer distribution).
The faster relaxation response was
predicted from the master curve (
Figure 1
),
which showed the rheological differences
of these two products in the low shear
range. When interpreting the data, it
is beneficial to have an understanding
of the cooling environment typical for
PVDF processing. In a standard jacketing
operation producing a 0.020" jacket and
run at 300 feet per minute with a 6" gap
between the cooling tank and the die, it
was estimated that the time from the end
of drawing and before entering the tank
will be 0.10 seconds, and the actual time
to solidify the jacket will be approximately
0.42 seconds for a total cooling time of
0.52 seconds. Based on this approximation,
the K2500-10 will have sufficient time
to relax after the drawing operation.
Conversely, the higher viscosity samples
as well as the non-random samples will
not have relaxed in this time period and
it would be assumed that the majority of
the elastic stresses will be frozen-in to the
resultant jacket. With the knowledge of
the rheological characteristics necessary
to achieve low shrinkage properties, and
analytical methods developed to screen
new materials, efforts to further improve
low shrinkage characteristics in PVDF have
been initiated.
PVDF structures already identified as having
low shrinkage characteristics were modified
for possible further improvement.
Two existing commercial grades of PVDF
identified as PVDF 1A and PVDF 2A were
characterised for shrinkback by conducting
a series of shrinkback experiments on
cables jacketed with these products.
Cable jackets were applied in-house using
a small lab extrusion line consisting of a
1-inch Killion extruder outfitted with a
BH-30 cross head and all the necessary
downstream equipment. Conditions such
as barrel temperature, water temperature,
line speed and tank distance were all
standardised to eliminate these as
variables in the experiment.
Cables were cut in 10-foot lengths and
the jackets were removed by slitting the
length of the cable. Shrinkback experi-
ments were conducted by measuring the
jacket length before and after a thermal
exposure of 121°C for 1 hour. A 24-hour
recovery period was allowed before taking
the final measurement.
Shrinkback experiments were repeated
using similar PVDF products having
some modifications to the structure
with the goal of further reducing shrink-
back characteristics. These samples are
identified as PVDF 1B and PVDF 2B. A
summary of the results from shrinkback
experiments can be found in
Table 3
.
▲
▲
Figure 2
:
Relaxation modulus of PVDF samples at 230ºC
PVDF Sample ID
Time (s) @ 100 Pa
Viscosity (Pa.s) @
80 s
–1
K2500-10
0.65
795
K3120-10
2.0
650
K2500-20
6.8
1460
K3120-15
10.0
1230
K2750-01
220
2290
K3120-50
400
2390
▲
▲
Figure 1
:
PVDF master curves – complex viscosity at 230ºC
▼
▼
Table 2
:
Stress relaxation at 230°C and 100 Pa