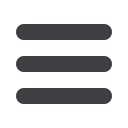

August 2015
MODERN MINING
15
MINING News
Hatch Goba designs Copperbelt mine shafts
The capability to design deep mine
shaft complexes, including ancillary
infrastructure such as underground
materials handling systems, has stood
Hatch Goba in good stead in complet-
ing a second major contract on the
Zambian Copperbelt.
Having successfully completed a
two-year detailed engineering design
project in 2013 for a 1 300-m deep
shaft (which comprised a shaft com-
plex with headgear, shaft steelwork,
winder house, underground materials
handling systems and a mine dewater-
ing pumping system), Hatch Goba was
subsequently awarded the detailed
engineering design for an expansion of
the same project.
Hatch Goba’s scope of work covers
two shafts, each about 2 000 m deep, to
allow the client to proceed with project
implementation. Hatch Goba Project
Manager Louis du Plessis states that
the aim is to access deeper parts of the
orebody and thereby reduce operating
costs.
“The detailed engineering design
of the two shaft complexes includes
the headgear, shaft steelwork, winder
house and underground materials han-
dling systems. Hatch Goba began work
in early 2013, with a projected comple-
tion date of June 2015 for the design
phase,” du Plessis comments.
“We were able to leverage off our
experience and incorporate it into
the expansion project, thereby saving
the client both time and engineering
design cost.” Hatch Goba has exten-
sive experience in this regard, having
designed numerous shaft complexes
over the years. “We have an excellent
track record, in addition to employing
highly skilled and competent people
in our Mining Business Unit,” du Plessis
confirms.
tively. The main north decline access is
approximately 60 m away from Block 11.
Mining access for both Block 10 and
Block 11 is scheduled for August 2015. On
the south mine, Block 16 is scheduled to
contribute to the ramp up phase.
Underground development and the
establishment of infrastructure towards
blocks that can benefit from mechanised
or partly mechanised hybrid mining has
been the focus for PTM and its contractors
over the past fewmonths. A conveyor from
1 423 m down the north decline to the ore
silo on surface and into the mill is expected
to be completed in October 2015. The
above ground portion of this conveyor has
now been completed.
The mill has been completed in accor-
dance with the original design and as
planned. The decision to add a MF-2 grind-
ing circuit on completed foundations,
thereby increasing capacity from 110 ktpm
up to a full 160 ktpm and take the mine up
to its planned 250 000 ounce 4E steady
state capacity, will be made as required
during 2017.