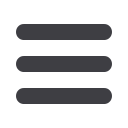

Technical article
September 2015
73
www.read-eurowire.comStandardisation of PV wires
and cables 2001-2014
By Faruk Yeginsoy, Leoni Struder AG
Abstract
This paper will show the evolution from
the first German TUV Rheinland document
2Pfg1169/2001 to 2Pfg1990/2012 and the
influence of this document to national
standards in the USA, Japan and Europe
as well as to the development of the
standards Cenelec EN50618 and IEC62930.
Furthermore it will give an insight to the
necessary design, material combinations
and production processes to comply with
the above stated standards.
In particular the challenge was to comply
with multiple standards as for example,
the combination of UL and TUV.
An additional aspect will give an
understanding to specific testing pro-
cedures of essential compound properties
which have an impact on the expected
very long operation time of PV wires.
1 Introduction
Starting at the end of the last century the
worldwide interest in renewable energy
was encouraging the PV industry to grow
significantly and this growth around
the world was irresistible. At that time
the construction of PV systems was an
expensive and long-term investment.
The investors did not know how to
estimate
the
quality
of
modules,
and customers were asking for the
expected lifetime of PV modules and PV
installations. There was a strong need for
a third-party assessment of safety and
quality.
At this time the German TUV Rheinland
started reviewing the safety and quality
of photovoltaic modules with their own
requirements.
Very soon it was clear that the module
quality and module safety was dependent
on the components, but there was a lack
of standards for components considering
the requirements of PV application. This
was the beginning of the standardisation
of PV wires.
2 The beginning
In 2001 the TUV Rheinland in Germany
started testing PV modules and noticed
many problems because of the cables.
Since no dedicated standard tests for
these cables existed, the TUV Rheinland
created their own standard. This was the
birth of 2Pfg1169:2004.
This first standard was based on
IEC60245-4:1994 (Rubber insulated cables
- rated voltages up to and including
450/750 V - Part 4: Cords and flexible
cables).
At that time H07RN-F was the most used
cable (rubber 60ºC–90ºC). In this early
stage of PV installations, nobody realised
that the requirements on PV cables were
much higher.
2.1 First wiring failures after
a few years
3 New requirements
After numerous wiring failures the PV
experts recognised that the requirements
of the first Pfg 1169 /2004 had been too
low.
In 2006 a new experts group (German
National Committee Working Group
411.2.3) started to work on a new version
of the “Requirements for photovoltaic
cables”.
In the first part of the work, it was a joined
group of module and cable experts. The
focus was now on the period of use of PV
wires. The working group was principally
involved in following questions:
• How can we predict the lifetime of a
cable?
• How many years does the lifetime of a
cable have to be?
• How is ageing of cables to be
understood?
• How can we test the ageing process?
3.1 Material ageing is the new focus
3.1.1 Thermo-oxidation of polyolefins
One of the elementary chemical laws is
the Arrhenius law. This law describes the
correlation of temperature and process
speed.
The thermal ageing of polymer is nothing
else than a chemical process, and every
chemical process is dependent on the
process temperature.
Increasing the temperature by 10°C
accelerates the process by a factor of two.
This also works backwards. Decreasing
the temperature slows down the ageing
process by a factor of 0.5.
The specified temperature rating of a cable
should be in combination to a specified
time period.
▼
▼
Figure 1
:
Wiring failures caused by ozone and high
temperatures