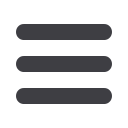

Technical article
September 2015
74
www.read-eurowire.comWithout a time indication, the temperature
rating is useless. The standard temperature
rating in the European cable industry is
xxx°C at 20,000h.
The PV industry standard period of use
for PV modules is 25 years. These are
roughly 150,000h. The assumed ambient
temperature is 90°C, ie the minimum
temperature rating shall be 90°C/150,000h.
Normalised to the industrial standard time
of 20,000h, the new temperature rating
shall be 120°C/20,000h.
3.1.2 Photo-oxidation
Sunlight contains a high amount of
ultraviolet
radiation. The
ultraviolet
radiation that is absorbed by a polymer
material will result in its degradation.
The energy may be sufficient to cause
the breakdown of the unstable polymer
and, after a period of time, changes its
components.
Polymer materials which are to be exposed
to UV for long periods of time should be
made from polymer compounds that
are appropriately stabilised for such
environmental conditions. The basic
polyolefin polymers have limited outdoor
life. However, most polyolefin, coloured
(non-black) solar cables manufactured
today contain an ultraviolet stabilisation
package which is satisfactory for limited
time of 5–10 years. But for prolonged
outdoor service life, polyolefins should be
formulated with a minimum of 2.5 per cent
finely dispersed carbon black.
Implementing carbon black in polyolefins
greatly increases the UV resistance. Carbon
black acts as a UV absorbent and screens
the polyolefin from damaging ultraviolet
radiation.
Until now there has been no known
physical or chemical interrelationship
applicable to extrapolate an accelerated
weathering test up to the lifetime of cables.
The conducted test durations in standards
UL and TUV are 720h whose results cannot
be extrapolated based on a mathematical
formula. These tests provide only compar-
able results, but no real statement about
the real lifetime.
As has been demonstrated through over
four decades of outdoor experience with
polyethylene jacketed communication
cables, the addition of 2.5 per cent finely
dispersed carbon black results in more
than 25 years of protection against UV.
The dispersion of carbon black is an
integrated part of the extrusion process of
the jacket, which has a high impact on the
UV resistance. The proper management of
the machine parameters is the critical key
factor for best results.
Carbon black is in EN50290 (“Communi-
cation cables. Common design rules and
construction“) a mandatory requirement
for communication cables for exposed
outdoor use.
3.2 Basic points of the new
requirements in 2007
The main basic point of the new version
of the Pfg1169/2007.8 is the thermal
endurance test according to IEC60216
“Electric insulating materials – Thermal
endurance properties” (120°C/20,000h).
In the application of this standard, it is
assumed that an almost linear relationship
exists between the logarithm of the
time required to cause defined property
change (less than 50 per cent elongation
at break) and the reciprocal value of the
corresponding absolute temperature.
This test is to conduct at least three
different
temperatures. The
highest
temperature shall be selected to result
an endpoint not less than 100h and the
lowest temperature is to be selected for
the expected result not before 5,000h.
A straight line is drawn to connect the
various recorded points. By extending
the line until it intersects the 20,000h on
the ordinate – axis (logarithm of time) it
is possible to determine the temperature
rating on the abscissa – axis (the reciprocal
absolute temperature).
Additional essential points are:
• The used materials shall be halogen-
free
• The used conductors shall comply with
IEC 60228 class 5
• The cables and wires have to comply
with IEC60332-1-2 (vertical flame test)
The result of this work was published by
VDE as:
• VDE-AR-E 2283-4 “Requirements for
cables for PV systems”
And by TUV as:
• TUV 2Pfg1169/2007.8 “Requirements
for cables for use in photovoltaic
systems”
3.3 The specification of PV wires by UL
In 2005 UL published the first edition of
Outline 4703. The UL type ‘PV’ was created.
This outline was based on UL854 (Service
Entrance Cables). But in 2005, the NEC2005
(Article 690) was requiring USE, USE-2, UF
and SE.
As recently as 2008, the PV type was
mentioned for the first time in the
NEC2008. The required wires were in this
edition USE-2 or PV.
Mentionable is the acceptance of metric
sizes of conductors in the UL outline 4703.
In 2010 UL published the fourth edition
of UL outline 4703, which is the relevant
version until today. In this edition is the
reference standard UL 44 “Thermoset-
insulated wires and cables”.
3.3.1 The differences to TUV 1169/2007.8
The significant differences between UL
and TUV are:
• Halogenated
compounds
are
permitted in UL4703
• The required flaming test UL1581-1060
is more demanding than IEC60332-1
• No differentiation between DC and AC
in UL4703
• 1,000V (or 2,000V) is permitted, which
is more future-orientated
• Aluminium wires are permitted in
UL4703
• No differentiation U0/U in UL4703
4 New challenge for
the cable industry
4.1 TUV and UL approved cables
2006–2013
In 2006 the module manufacturers started
to think globally. The new marketing
requirement was to manufacture one type
of photovoltaic module with all relevant
approvals to sell them on all markets. The
challenge was to create a cable which
could combine the opposed specifications
of UL (PV / USE-2) and TUV 1169. Particularly
the following discrepancies had to be
overcome.
• Halogen-free compounds are highly
filled with flame retardant minerals.
The physical properties required by
UL are a challenge for this kind of
compound
• Passing the flame test required by UL is
easy for halogenated compounds but
difficult for halogen-free compounds
• The long-term stability test of UL is a
real challenge for filled compounds
because the flame-retardant additives
are hygroscopic
However, it was possible to comply with all
these requirements.
4.1.1 The first solution
The outstanding characteristics of this
design are:
• Three-layer extrusion in one pass
(implicated by increasing pricing
pressure in the PV industry)
▲
▲
Figure 2
:
Definition of U
0
/U
GND