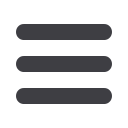

Technical article
September 2015
75
www.read-eurowire.com• Special
developed
polymer
as
separator
• Separable layers which have been
required by many customers (UL
definition:
“Thermoset
insulation
having a jacket”)
• The
difference
of
these
two
cable families are different layers
thicknesses because the UL has a
higher requirement for the insulation
thickness
• All
compounds
are
thermoset
(electron beam crosslinking)
5 The next step
5.1 New requirements
In 2013 the new requirement of the PV
industry was to increase the system
voltage to save cable cost and to increase
the efficiency of the PV systems. The
voltage rating of the first generation of
PV wires according to TUV1169 was based
on generic industrial cable standards. The
standard voltage rating of low voltage
cables in the CENELEC and IEC is U0/U =
600/1,000V AC or 900/1,500V DC.
The nominal voltage rating of the new
generation photovoltaic wire is U0/U =
1,000/1,000V AC or 1,500/1,500V DC. In
the meantime TUV Rheinland developed
2Pfg1990/2012, which considers the new
requirements.
5.2 New generation of UL4703 1,000V/
TUV 1,500V DC cables
The outstanding characteristics of this
design are:
• Four-layer extrusion in one pass
(implicated by further increasing
pricing pressure in the PV industry)
• All
compounds
are
thermoset
(electron beam crosslinked)
• Layers not separable (UL definition:
“Composite insulation without a
jacket”)
• Approvals: UL (1,000V)/TUV (2Pfg1990)/
CSA 22.2 No. 271-11
6 The way to CENELEC
and IEC
6.1 CENELEC
In 2011 the German National Committee
for PV wires and cables started to work
out a revision of VDE-AR-E 2283-4
“Requirements for cables for PV systems”.
The target was now to apply this draft
as a new work item to CENELEC TC20. The
main topics were:
• Increasing the system voltage
• Adapting test procedures to the new
voltage level
The result of this work is EN50618, which
was published as a final draft in August
2014.
6.2 IEC
In 2013 IEC adopted the draft EN50618
on request of IEC TC82 as a basic paper
to start to work out an IEC standard for
photovoltaic wires.
This is now published as a committee draft
IEC62930.
The IEC draft is 95 per cent identical to
EN50618.
6.2.1 The difference to EN50618
The main difference between EN 50618
and IEC 62930 is that in the IEC standard
class two conductors are permitted for use
for fixed installations.
7 What is new in
EN50618 and IEC
62930
7.1 Design
There are no great differences in the
design requirements of these new
standards. Notice, however, the definition
of black as preferred jacket colour.
Minor changes are in the required layer
thicknesses, which are slightly increased.
7.2 Test requirements
Note that the material testing procedures
have been widely changed by adapting
IEC60811 ”Electric and optical fibre cables
– Test methods for non-metallic materials”.
• All test samples now have to be taken
from finished cables
• It is not permitted to conduct material
tests on extruded tapes or moulded
plates
Paper courtesy of the 63
rd
IWCS Technical
Symposium, Providence, Rhode Island, USA,
November 2014.
▲
▲
Figure 3
:
Optimised design of a UL4703 and
TUV1169 or TUV1169 wire
▲
▲
Figure 4
:
New design
Jacket
Separator
Insulation
Conductor
Two-layer jacket optimised for
mechanical properties and flame
retardance
Two-layer insulation. Electrical
properties and flame retardance
Conductor
Leoni Studer AG
Business Unit Solar &Windpower
Däniken
Switzerland
Tel
: +41 799138728
:
faruk.yeginsoy@leoni.comWebsite
:
www.leoni.com