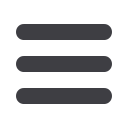
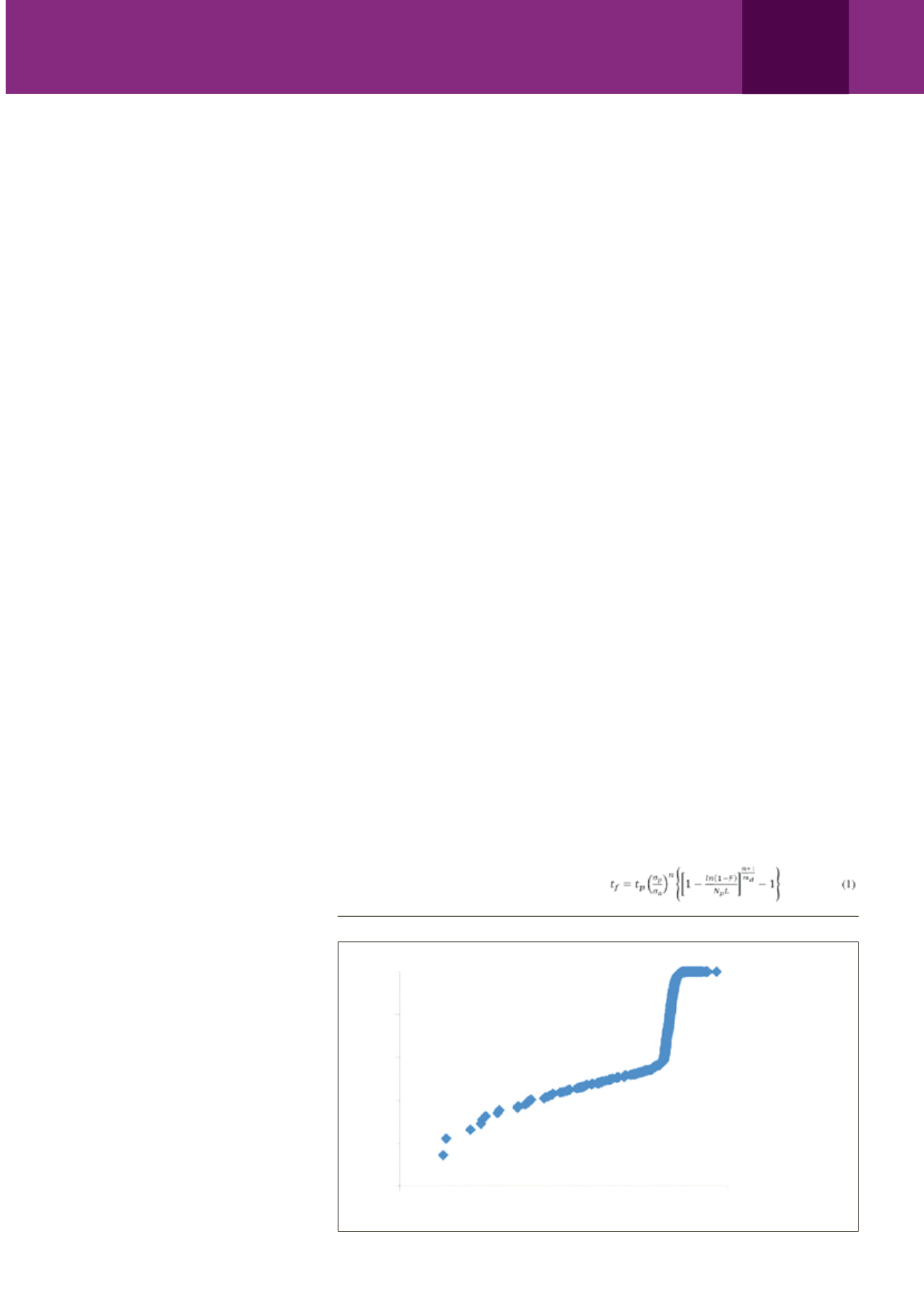
Technical article
March 2015
87
www.read-eurowire.com2.4 Cutting costs by minimising
material in the cable and reducing
design margins
Many overhead cables are designed with
zero per cent strain on the optical fibre. With
increased cost pressure, design engineers
are challenged to reduce material costs.
As strength elements around the optical
fibre are removed, the optical fibre starts to
take some of the axial strain traditionally
taken by the strength members in the
cable. The design engineer can look to the
various cabling standards and see that
the maximum allowable long-term strain is
20 per cent of the proof test level.
In effect, for these cables, the industry
is progressing from a common design
practice where no strain was carried by
the optical fibres after installation to one
where a strain of up to 20 per cent of the
proof test level is allowed. The long history
of reliable cable performance at this strain
level makes it seem a reasonable decision.
2.5 Higher proof-tested fibres 1.38 GPa
(200 kpsi) are now available
In the previous section it was shown that
material costs can be reduced by allowing
strain on optical fibre. For traditional
optical fibre that is proof tested at 0.69
GPa (100 kpsi), the maximum allowable
strain on the fibre at the 20 per cent limit is
0.14 GPa. A design engineer could choose
to use higher proof-tested fibre, such as
1.38 GPa (200 kpsi) fibre, at the 20 per cent
limit, and the allowable strain on the fibre
after installation would increase to 0.28
GPa. This would allow further material
reductions in the optical cable by allowing
greater cable strain to impart twice the
strain on the optical fibre. The net result
could be a lower cost optical cable.
2.6 Combined impact of modified
optical cable design criteria
Taken together, all these trends can result
in a scenario that may not be optimal to
the service provider. The strain on the
fibres allowed by the usual criteria is
higher, but the strain is not impacting the
attenuation because of the use of G.657
fibres. The net result could be an optical
cable that is deployed with up to 0.28
GPa long-term strain on the optical fibres.
Meanwhile, there remains an expectation
that the fibres will survive 30+ years
without breaking. This situation tests
the limits of reliability theory and should
be looked at more closely before it is
implemented.
3 Origin of the current
allowable strain
criterion
The current rule of thumb used for cable
design is a maximum allowable strain of
20 per cent of the proof test level. This
criterion comes from the reliability work
done in the 1990s
[2,3]
. In those studies, the
authors show that long-term performance
can be related to the proof test stress, but
this assumes a certain proof test failure
probability. They, then, look at various
stress corrosion parameters and at 50 kpsi
and 100 kpsi proof-tested fibre to show
that their approximation is a reasonable,
conservative method to ensure long-term
reliability. This work was an important
step forward for the fibre industry and
supported the move for proof-testing fibre
at the current levels.
Unfortunately, there is a key assumption
about the flaw distribution of the optical
fibre – specifically the chance of a
fibre breaking when proof-tested. This
probability is not constant and can vary
for fibres manufactured under different
conditions or using different raw materials.
Figure 1
shows a failure probability curve
for silica fibre generated by one of the
authors’ facilities using 10m gauge length
to illustrate the range of flaws found in
optical fibres.
The figure shows two regions: region I
(intrinsic strength) and region II (extrinsic
strength). The curve illustrates the main
regions that need to be characterised to
predict long-term fibre reliability. Region I
is the high strength intrinsic region.
The fibre investigated showed the
inherent strength of the glass at ~4.6 GPa,
which is significantly above the limit of
3.1 GPa recommended in Telcordia GR-20.
Short gauge-length strength testing in
this region can be used to determine the n
value, which is greater than 20 for the fibre
investigated. The intrinsic strength and n
values are typically specified by end users
to ensure long-term reliability of the cable.
Unfortunately, the extrinsic portion,
shown as region II, plays an important role
in characterising the long-term reliability
of an optical cable. This region contains
flaws closer to the proof-test level that
are spaced at a frequency which may be
several kilometres apart.
Over time, these can become fibre
breaks if the cable is left in tension.
Understanding
this
region
requires
information that can only be gathered
by measuring many kilometres of fibre.
Higher proof test levels will eliminate
some of the larger flaws in the fibre.
However, the exact impact to optical fibre
reliability in a deployed cable is hard to
determine without more information on
the overall flaw distribution in the fibre.
One way to illustrate this would be to
proof-test an optical cable at a level
just shy of the intrinsic strength of the
fibre, or about 3.8 GPa (550 kpsi). If a
1,000m fibre sample generated from that
experiment were left at a constant stress
of 110 kpsi, the fibre would likely break in
less than a day, or well in advance of the
40-year expected life time. This example
is an extreme case, but highlights the
importance of understanding the complex
equations that govern reliability.
4 Guidance from IEC
technical report on
reliability
One of the currently accepted reliability
models has been published by the IEC
[4]
.
One of the equations found in that report
is used to predict fibre lifetime – the
lifetime equation for optical fibre after
proof testing. This can be shown as the
following expression:
Log (failure probability)
Log (stress)
Region II Extrinsic
Region I Intrinsic
▼
▼
Figure 1
:
Failure probability for over 100km of fibre tested at 10m gauge lengths