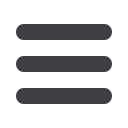

87
article technique
EuroWire – Septembre 2010
et le chrome améliorent la résistance à
la corrosion d’un alliage de cuivre, ils en
réduisent toutefois considérablement la
conductivité (voir
Figure 1
).
Les éléments composites représentent
une solution fréquemment adoptée
pour résoudre ce problème, surtout sous
forme de revêtements à base d’étain pur
appliqués à la surface de l’alliage de cuivre.
Seulement dans les cas de rares exceptions,
la directive RoHS (Restriction of Hazardous
Substances), concernant l’utilisation de
certaines substances dangereuses dans
l’équipement électronique et électrique,
entrée en vigueur le 1
er
juillet 2006, interdit
les composés classiques de plomb-étain
qui
étaient
utilisés
auparavant.
L’intégration du revêtement fonctionnel
d’étain pur dans le cycle du matériau est
décrit en détail ci-après
La sélection du matériau pour les
connecteurs est principalement basée sur
des critères physiques tels que la conduc-
tivité électrique, le module d’élasticité, la
relaxation thermique et les caractéristiques
de processus telles que la ductilité
et la capacité de pliage ainsi que le
comportement au soudage. Les problèmes
concernant la protection partielle ou
totale de la surface sont d’importance
secondaire de même que la disponibilité
de base des matériaux et les coûts des
ces derniers.
Une analyse des déchets de production et
de poinçonnage révèle que, dans plusieurs
cas, ces facteurs ne sont pas suffisamment
considérés ni du point de vue écologique
ni du point de vue économique ainsi
que l’illustre l’exemple suivant. Durant
la production de grille de connexion de
grandes dimensions réalisées en CuFe2P
(C19400) étamé par immersion à chaud
pour les systèmes ABS et ESP, on produit
environ de 50% à 70% de ferraille.
Cette dernière ne peut pas être
directement recyclée (réintroduite dans le
processus de fusion), elle doit être soumise
à des processus de fusion et de séparation
électrolytique exigeant beaucoup de
temps.
La ferraille est ensuite réintroduite dans
le cycle de matériau et de production
sous forme de cathode. Ce procédé
est caractérisé par une forte intensité
d’énergie et est donc coûteux quant à la
fusion directe.
Généralement, une bande d’une épaisseur
de 0,4mm est pourvue d’un revêtement
d’étain de 3µm sur les deux côtés. Lorsque
la ferraille est recyclée directement, l’alliage
de CuFe2P en résultant contient environ
1,5% d’impuretés d’étain. Cela influence
considérablement le comportement durant
l’écrouissage et la conductivité électrique
de l’alliage, qui diminue drastiquement
lorsque la teneur en étain dépasse 0,3%
(
voir la Figure 2
).
Il est donc nécessaire d’avoir un nouvel
alliage avec des propriétés comparables à
celles du CuFe2P, mais pouvant être recyclé
sans difficulté, même lorsqu’il est revêtu
d’étain. Les alliages de cuivre pur et d’étain
tels que le CuSn 0.15 offrent la possibilité
BB01 C14410/15
SB02 C19400
BB05xi
Cuivre
Balancement
Balancement
Balancement
Étain
0.12
-
0.2 – 0.8
Zinc
<0.10
0.13
<0.05
Fer
<0.02
2.4
<0.02
Nickel
<0.02
–
0.1 – 0.6
Phosphore
<0.015
0.03
0.008 – 0.05
BB01
SB02
BB05xi
Conductivité électrique
douce [% IACS ]
>83
63
>62
Conductivité thermique
(watts/mètres Kelvin)
360
260
250
Coefficient d’expansion
thermique [Rt-100°C]
17.7 x 10
-6
17.7 x 10
-6
17.7 x 10
-6
Module d’élasticité
[GPa]
128
123
126
Épaisseur de la bande 0,3mm
BB01
SB02
BB05xi
Rm [MPa]
450
450
425
Rp
0.2
[MPa]
410
420
380
A50 [%]
4
9
6
HV
130
145
125
Température de ramollissement
[ºC (1 h)]
300
350
350
Capacité de pliage
[180º GW R/S]
1
0
0.5
Capacité de pliage
[180º BW R/S]
1
1
0.5
Teneur en étain en %
Conductivité électrique relative en %
Figure 2
▲
▲
:
Influence de la teneur en étain sur la conductivité du CuFe2P
Tableau 1
▲
▲
:
Comparaison de la composition chimique de différents bronzes
Tableau 2
▼
▼
:
Comparaison des propriétés technologiques de différents bronzes
Tableau 3
▼
▼
:
Comparaison des propriétés technologiques de différents bronzes