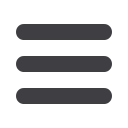

Article technique
Septembre 2017
85
www.read-eurowire.comdimensionnel de 1:75. Si l’on ajoute la
limite d’élasticité de 200 à 1 050N/mm², le
rapport à contrôler est de 1: 390.
En raison de ce large spectre, la traction
de la bande est mesurée directement
sur le dérouleur et sur l’enrouleur ainsi
que devant la machine à dresser et fait
office de valeur de contrôle pour les
actionnements. Ceux-ci sont équipés de
moteurs CA hautement dynamiques.
La capacité installée s’élève à environ 550
kW. «L’alimentation est effectuée avec
les ensembles Sinamics S120 Basic Line,
de sorte que l’énergie de régénération
puisse être réutilisée via un système de
récupération énergétique placé sur le
côté de traction, dans les cas des moteurs
positionnés en aval de la planeuse.
Cela permet de réaliser d’importantes
économies d’énergie», a ajouté M.
Lüdec, en soulignant l’un des principaux
avantages de la ligne. L’activation est
effectuée par des inverseurs entièrement
numériques, qui sont couplés à l’API du
contrôleur de ligne via Profibus L2-DP.
Les fonctions de commande effectives
sont contrôlées via un microprocesseur
permettant non seulement une facilité
de
fonctionnement
considérable,
mais également un démarrage et une
maintenance aisés.
Un concept
opérationnel
particulièrement
convivial et sûr
La ligne complète porte le marquage CE
et est conçue conformément à la directive
machines européenne 2006/42/CE, qui
prévoit, entre autres, une clôture de
protection pour la sécurité des employés.
L’existence
de
plusieurs
zones
de
protection
signifie
que
l’opérateur
peut déjà exécuter les activités dans
l’une d’elles alors que les mouvements
automatiques sont encore en cours
d’exécution dans une autre. Lorsqu’un
tel sous-secteur est ouvert, la vitesse est
automatiquement réduite à un niveau de
sécurité.
«De plus, en raison de la disposition
spatiale des consoles, une distance
suffisante des pièces de la machine en
mouvement et de la bande est assurée
par le type de conception adopté», a
déclaré M. Lüdecke. La durée normale
jusqu’à l’arrêt est de 12 secondes, mais
elle peut être réduite à 6 secondes ou, en
cas d’urgence, voire même à 3 secondes si
nécessaire.
Du point de vue de l’opérateur, le matériau
se déplace de gauche à droite à travers
l’installation à une vitesse allant jusqu’à
300m/min. Les étapes individuelles du
processus sont affichées au moyen d’une
vue d’ensemble et d’images détaillées.
L’opérateur peut entrer directement les
données via des boutons et des champs
de données dans les images ou via des
fenêtres surgissantes.
Les positions des axes typiques pour les
matériaux peuvent être mémorisées sous
la forme de jeux de données avec des
noms alphanumériques dans une base de
données.
Il est en outre possible d’intégrer dans
le système la gestion des commandes
personnalisées pour les clients. La
connexion au réseau de l’entreprise
garantit à l’opérateur l’accès à son plan de
production courant à tout moment.
En cas de changement de cassette, le
système reconnaît quelle casette est
actuellement installée au moyen d’un
système d’identification.
Aucun réglage manuel exigeant une perte
de temps n’est donc plus nécessaire. Grâce
à d’autres systèmes automatiques, par
exemple le bobinage automatique et le
transport de couronnes et de bobines,
il est possible d’exécuter des activités
parallèles.
En conséquence, des activités, qui avant
exigeaient la présence de deux hommes
pour l’exécution, peuvent être maintenant
réalisées par un seul opérateur.
Un système d’alimentation développé par
B+S contribue également à la rentabilité
et à la convivialité: dans ce cas, la bande à
traiter est montée comme d’habitude sous
la forme d’une couronne sur le dérouleur.
L’alimentation manuelle n’est cependant
pas nécessaire. Au contraire, le début de
la bande est bloqué dans une barre de
serrage au début de la ligne et tiré jusqu’à
la sortie à une vitesse de 10 à 15m/min.
Cela signifie qu’aucune bande pilote
n’est nécessaire et que le soudage et les
plaques de guidage sont éliminés.
L’enroulement
initial
sur
l’enrouleur
s’effectue également automatiquement
moyennant un enrouleur à ceinture. «La
productivité de la ligne a augmenté, car le
traitement effectif peut démarrer de façon
rapide et efficace», résume le responsable
technique.
Pour s’assurer que la bande est
soigneusement enroulée à son extrémité,
le dérouleur et l’enrouleur sont également
équipés d’un système de réglage du bord
de la bande. Les dévidoirs, chacun pesant
six tonnes, sont installés sur des guides
linéaires préchargés, sans jeu et montés
sur des paliers à roulement.
Outre la détection du bord et le contrôle
de la position, les dévidoirs assurent un
déroulement et un enroulement précis à
l’aide d’un vérin hydraulique à commande
servo-hydraulique.
n
Burghardt + Schmidt GmbH
Raiffeisenstraße 24, 75196 Remchingen,
Allemagne
Tél
:
+49 7232 36610Fax
:
+49 7232 3661 65:
info@b-s-germany.deWebsite
:
www.b-s-germany.de