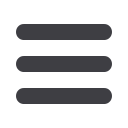

July 2008 Tube Products International
27
developments
products &
Flat rolled and spiral welded
US Steel Košice sro, a subsidiary of
USS Corporation, is a producer of flat
rolled products with an annual production
capability of 4.7 million tons. The company
produces a wide assortment of hot rolled,
cold rolled and coated sheets designated
for various industries. In addition to flat
rolled products, the company produces
spiral welded pipes using structural and
micro-alloyed hot rolled sheets.
The dimensional range varies in diameters
from 406mm to 1,420mm, with wall
thickness from 5mm to 14.2mm and lengths from 8 to 18m. The company
has been producing spiral welded pipes since 1960. Its pipes have been used
in major projects, such as the world largest oil pipeline, ‘Druzhba’, and gas
pipeline ‘Bratstvo’. Over 23,800km (14,800 miles) of pipes have been produced,
representing 3.352 million tons supplied to almost all European countries and
former Soviet Union countries.
The company takes advantage of its strategic location in the heart of the
continent for exporting its products to many European countries and beyond.
The pipe mill produces approximately 90,000 tons per year. These pipes are
used mainly for gas distribution lines, crude oil and water distribution lines, for
district heating and cooling systems and for civil engineering and structural
purposes. All pipes are produced in conformity with the internationally
recognised standards API, EN and DIN. The entire production process is
continuously monitored, the pipe surface and welds are consistently controlled
by series of non-destructive tests, and all results are archived.
US Steel Košice sro
– Slovak Republic
schytilova@sk.uss.com•
www.usske.skUS Steel Košice produces spiral
S
S
welded pipes, in addition to flat
rolled products
New grinding
machine installed
Engineering support organisation Corus
Northern Engineering Services (CNES),
UK, has built and installed a large
grinding machine for Wyman-Gordon
Ltd, a manufacturer of seamless pipes
for the offshore oil, gas and power
generation industry based in Livingston,
Scotland.
The new grinding machine, which
measures 19m in length by 2.5m wide
and 4.5m high, weighs approximately
70 tonnes and has a 16m travel for the
grinding heads. The machine is part of a
significant capital investment expansion
project at the company’s Livingston
site, and will supplement the company’s
original grinding machine (which is more
than 40 years old), to help to reduce
lead times for process pipe.
The machine will be used to grind the
outside diameter of seamless pipes,
which vary in length from 5m to 12m,
with diameters from 200mm to 1,200mm
(as long as the weight does not exceed
15 tonnes). The grinding machine grinds
the outside casing to give a smooth, flat
finish to the pipe.
Wyman-Gordon manufactures a range
of Class 1 rotating parts for military, civil
and industrial gas turbine applications.
These products include gas turbine
engine shafts, structural and landing
gear forgings for military and civil
aircraft, as well as manifolds, sphere
tees, valve bodies and seamless pipes
for the offshore oil and gas industries.
Themajority of the newmachine (in terms
of weight) is in the rails and travelling
beam, which had to be lifted in one piece,
requiring the use of heavy-duty lifting
gear. Chris Morris, senior plant engineer
at Wyman-Gordon, commented,
“CNES
handled the job extremely well and there
were few problems during the project.
After visiting the Scunthorpe workshop,
we were very confident that CNES
could handle the work. The workshop
had a very professional feel to it, was
organised and clean, the approach and
organisation were excellent and material
was flowing through the workshop.”
CNES received the contract to build
the new machine in May 2007. The
machine was built and ready to ship in
November, and delivery and installation
– also undertaken by CNES – took place
in December. The grinding machine has
since been placed inside an acoustic
chamber at the plant, and has just
completed commissioning.
CNES, part of the Corus Group Plc,
uses a ‘toolbox’ of techniques to help
customers of all sizes and from various
industry sectors maintain their output,
efficiency and profitability, by providing
a detailed and accurate assessment of
their plant assets. The company uses
a range of non-intrusive techniques,
including
acoustic
monitoring,
thermographic imaging, vibration
monitoring, laser alignment, lubricant
technology and remote visual inspection.
CNES also offers structural design,
project management, training, electrical
and process control, machining, fitting
and weld reclamation services.
Corus Northern Engineering Services
– UK
cnes@corusgroup.com www.corusnes.comWyman-Gordon Ltd
– UK
www.wyman-gordon.comWyman-Gordon’s new grinding machine
S
S
will help reduce lead times for the
company’s process pipe