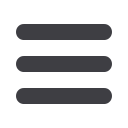

Articolo tecnico
Marzo 2013
117
www.read-eurowire.coma 3,8pf/ft. Questi risultati dimostrano che i
problemi di prestazione, spesso attribuiti
al fluoropolimero, sono tipicamente
problemi
di
processo
legati
agli
equipaggiamenti. L’utilizzo di un iniettore
mal dimensionato o di una struttura
instabile può mascherare il reale beneficio
delle prestazioni di alcuni materiali.
Raffreddamento del
prodotto
Il mezzo di raffreddamento per il nucleo
estruso è generalmente costituito da
una combinazione di aria ambiente e
acqua. La distanza richiesta per ciascuna
di queste dipende dalle dimensioni del
prodotto e della velocità della linea. Le
distanze corrette sono fondamentali per il
raffreddamento prima dell’avvolgimento
del filo per evitare l’appiattimento
dell’isolamento sull’aspo e di influenzare le
prestazioni elettriche.
Mantenendo la distanza del punto di
raffreddamento dell’acqua il più possibile
lontano dalla testa di iniezione si otterrà
il prodotto migliore. Questo perché
una sufficiente distanza dal punto di
raffreddamento mediante aria consente
la contrazione della resina sopra il
conduttore
fornendo
un’interfaccia
uniforme e aderente al conduttore senza
necessità di eccessivo preriscaldamento.
Con tale interfaccia del conduttore
uniforme si ottiene una forza uniforme
del
nastro
di
isolamento
persino
dopo la rottura del legame iniziale. I
vantaggi consistono in una migliore
attenuazione di riflessione strutturale
e resistenza alle sollecitazioni delle
operazioni di processo successive. A
volte non si può applicare una sufficiente
distanza dal punto di raffreddamento
mediante ARIA in quanto la distanza di
raffreddamento complessiva disponibile
non è sufficiente. In questo caso, si deve
evitare l’utilizzo di acqua fredda nella
prima sezione di raffreddamento poiché
ne potrebbe conseguire un’eccessiva
ovalità dell’isolamento e una ridotta
adesione al conduttore. Si raccomanda un
raffreddamento temprato poiché riduce lo
shock iniziale nell’isolamento migliorando
la sua ovalità e adesione al conduttore.
Skinning
L’estrusione di uno strato esterno di
materiale solido o skinning offre dei
benefici aggiuntivi quali:
• un modo facile ed efficiente di colorare
l’isolamento
• una resistenza dielettrica migliorata,
che è utile nelle strutture di cavi con
pareti più sottili
DuPont Chemicals
and Fluoroproducts
1007 North Market Street
Wilmington, Delaware
USA
Tel
: +1 302 774 1000
Website
:
www.dupont.com:
www.info@dupont.com▲
▲
Figura 6
:
Sezione trasversale di un nucleo di
schiuma con strato solido esterno
• tassi di espansione della schiuma più
alti
• maggiore
resistenza
ai
danni
dell’isolamento durante il processo
successivo
come
cordatura
o
trecciatura
L’applicazione di un rivestimento solido
richiede un investimento iniziale in
equipaggiamenti (un estrusore ausiliario
e una testa di iniettore speciale), ma offre
benefici mediante una riduzione degli
scarti e dei costi di prodotto. La schiuma
e lo strato solido si ottengono allo stesso
tempo mediante una testa di iniettore
singola utilizzando metodi di processo
standard. La
Figura 6
illustra un nucleo
di schiuma con uno strato esterno solido
colorato.
Conclusioni
Vi sono diverse opzioni di resine di
fluoropolimero espandibile disponibili, e
ciascuna presenta possibilità e limitazioni
specifiche. La scelta della resina corretta
per l’applicazione specifica è importante
per i costi, per facilitare il processo e
per ottenere le prestazioni elettriche
desiderate.
La progettazione e la lavorazione dei
cavi considerando le caratteristiche dei
materiali consente di ottenere prodotti
con alti rendimenti.
La selezione degli equipaggiamenti di
processo e le condizioni di processo sono
fondamentali per garantire un processo
stabile, mantenere una minima variazione
del prodotto e ridurre il più possibile i
costi dell’operazione. Tecniche speciali
quali l’aggiunta di uno strato o più strati
di rivestimenti solidi alle strutture espanse
possono migliorare ulteriormente il
processo e le prestazioni.
n
L’iniettore
selezionato
per
questo
processo richiede che l’orifizio abbia
dimensioni adeguate per ottenere una
portata di gas di 50cc/minuto ad una
pressione superiore alla pressione del
tamburo. Con un flusso superiore a 50cc/
minuto a 1.000psig, la pressione del gas
dovrebbe essere regolata ad un valore
inferiore alla pressione del tamburo;
ma in questo modo si produrrebbe
l’ostruzione dell’iniettore con conseguente
solidificazione del prodotto. Aumentando
la pressione del gas a valori superiori a
1.000psig, il flusso del gas sarebbe troppo
elevato e l’espansione sarebbe eccessiva.
Questa eccessiva formazione di schiuma
viene spesso fraintesa e considerata
un problema dovuto al materiale o al
processo.
Al contrario, se l’orifizio dell’iniettore
è troppo piccolo, la pressione del
gas disponibile potrebbe non essere
sufficiente per ottenere il flusso di gas
richiesto. Ciò comporterà l’impossibilità
di ottenere il tasso di espansione e la
capacitanza del prodotto desiderati.
Generalmente, per questa ragione si
utilizzano diversi iniettori con vari flussi
disponibili per un’ampia gamma di
pressioni. Il numero di diverse dimensioni
necessarie varia secondo la gamma di
prodotti e la pressione del gas disponibile.
L’utilizzo di una pompa di azoto ad alta
pressione aumenta la gamma di pressioni
di gas disponibili rispetto all’utilizzo di un
cilindro ad alta pressione. L’utilizzo di una
pompa può pertanto ridurre il numero di
dimensioni degli iniettori richiesti per una
operazione con conseguente riduzione dei
costi complessivi.
Anche la struttura dell’iniettore può
influenzare le prestazioni. La
Figura
5
illustra i risultati delle prove basate
sulla comparazione di quattro tipi di
iniettori disponibili sul mercato ottenuti
misurando la variazione del flusso del gas
e la variazione della capacitanza risultante.
Per queste prove è stato utilizzato un
nucleo di 50Ohm con un conduttore di
diametro 23G espanso fino a circa il 50
per cento. La variazione Sei Sigma del
flusso di gas (± 3 deviazioni standard)
variava da 4cc/min a 27cc/min con una
variazione di capacitanza risultante da 0,3