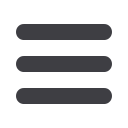

Artículo técnico
Marzo de 2013
123
www.read-eurowire.comEl diseño del inyector puede afectar
también a las prestaciones. La
Figura 5
muestra los resultados de pruebas en las
que se comparan cuatro tipos de inyectores
comercialmente disponibles obtenidos
midiendo la variación del flujo del gas y
la variación de la capacitancia resultante.
Para estas pruebas se usó un núcleo de
50Ohm con un conductor de diámetro 23
expandido aproximadamente a un 50%.
La variación Seis Sigma del caudal del
gas (± 3 desviaciones estándares) iba de
4cc/min. a 27cc/min. con una variación
de capacitancia resultante de 0,3 a 3,8pf/
ft. Estos resultados demuestran que los
problemas de prestaciones a menudo
atribuidos al fluoropolímero normalmente
son debidos a problemas de procesado
relacionados con los equipos. El uso de un
inyector mal dimensionado o un diseño
inestable puede ocultar las prestaciones
reales de ciertos materiales.
Enfriamiento
del producto
Normalmente, el núcleo extruido es
enfriado mediante aire ambiente mezclado
con agua. La distancia requerida para
cada uno de estos medios depende de las
dimensiones del producto y de la velocidad
de línea. La aplicación de la distancia
correcta es un factor fundamental para
el enfriamiento anterior al enrollado del
alambre a fin de evitar que el aislamiento se
aplaste en el carril y se afecte al rendimiento
eléctrico. Manteniendo la distancia del
punto de enfriamiento del agua lomás lejos
posible del cabezal inyector se obtiene un
producto mejor.
El motivo de esto es que una distancia del
punto de enfriamiento con aire grande le
da tiempo a la resina a contraerse sobre el
conductor formando una interfaz uniforme
y pegada al conductor sin necesidad de un
precalentamiento excesivo.
Con una interfaz del conductor uniforme se
obtiene una fuerza uniforme de la banda de
aislamiento incluso después de la rotura del
enlace inicial. Las ventajas que se obtienen
son una pérdida de retorno estructural
mejorada y resistencia a las tensiones de las
operaciones de procesado siguientes.
A veces, no es posible aplicar una distancia
del punto enfriamiento con aire suficiente
debido a la distancia de enfriamiento
total disponible. En este caso no se debe
usar agua fría en la primera sección de
enfriamiento, porque se puede causar una
ovalidad del aislamiento excesiva y poca
adhesión al conductor. Se recomienda un
enfriamiento templado porque reduce el
choque inicial en el aislamiento y se mejora
su ovalidad y adhesión al conductor.
DuPont Chemicals
and Fluoroproducts
1007 North Market Street
Wilmington, Delaware
EE.UU.
Tel
: +1 302 774 1000
Website
:
www.dupont.com:
www.info@dupont.com▲
▲
Figura 6
:
Sección de un núcleo esponjado con capa
externa sólida
Capa sólida externa
(
skinning
)
La extrusión de una capa externa de
material sólido o
skinning
proporciona
beneficios adicionales como:
• coloreado del aislamiento facilitado y
eficiente
• resistencia dieléctrica mejorada, que es
útil en diseños de cables con paredes
más finas
• tasas de expansión de la espuma más
altas
• mayor resistencia del aislamiento
contra daños durante el procesado
sucesivo como el pareado o el trenzado
La aplicación de un revestimiento sólido
requiere una inversión inicial en equipos
(una extrusora auxiliar y un cabezal
inyector especial) pero aporta beneficios
como la reducción de desechos y coste del
producto. La espuma y la capa sólida se
obtienen al mismo tiempo a través de un
solo cabezal inyector usando métodos de
procesado estándares. La
Figura 6
ilustra un
núcleo de espuma con una capa externa
sólida de color.
Conclusiones
Hay varias opciones de resinas de
fluoropolímero expandible disponibles,
y cada una presenta capacidades y
limitaciones específicas. Seleccionar la
resina adecuada para la aplicación es
importante para los costes, para facilitar el
procesamiento y obtener las prestaciones
eléctricas deseadas. El diseño y procesado
de cables considerando las características
de los materiales permite obtener
productos de alto rendimiento.
La selección de los equipos de procesado
y las condiciones del proceso son críticos
para asegurar un proceso estable,
mantener la variación de producto mínima
y reducir los costes de operación.
Técnicas especiales como el añadido de
de capas sólidas a estructuras expandidas
pueden aportar otras mejoras al procesado
y a las prestaciones.
n
respecto a la velocidad de avance del
producto. El caudal del gas depende de
las dimensiones del orificio del inyector
y de la presión del nitrógeno gaseoso.
El orificio debe ser dimensionado de
manera que la presión del gas sea más
alta que la del tambor para obtener el
flujo de gas deseado. Supongamos que
una determinada construcción de cable
requiere un caudal de 50cc/min. de
nitrógeno para una velocidad de línea de
600 pies/min. y genera una presión en el
tambor del extrusor de 1.000psig.
El inyector seleccionado para este
proceso necesita que el orificio tenga las
dimensiones adecuadas para entregar
un caudal de gas de 50cc/minuto a una
presión mayor que la del tambor. Con un
caudal mayor de 50cc/minuto a 1.000psig,
la presión del gas debe ser ajustada
para que sea más baja que la presión del
tambor; pero de esta manera se produciría
la obstrucción del inyector llevando a la
solidificación del producto. Aumentando
la presión del gas a valores superiores a
1.000psig, el flujo de gas sería demasiado
alto y el esponjado sería excesivo. Este
esponjado excesivo a menudo no es
aceptado bien porque es considerado un
problema debido al material o al procesado.
Por el contrario, si el orificio del inyector
es demasiado pequeño, la presión de gas
disponible puede ser insuficiente para
obtener el flujo de gas necesario, y como
resultado no sería posible conseguir la
tasa de expansión y la capacitancia del
producto deseadas.
Por esta razón, normalmente se tienen
varios inyectores de distintos caudales
disponibles para una amplia gama de
presiones. La variedad de tamaños
requerida depende de la gama de
productos y la presión del gas disponible.
El uso de una bomba de nitrógeno a alta
presión aumenta el campo de presiones
disponibles respecto al uso de un cilindro
a alta presión.
Por tanto, el uso de una bomba puede
reducir la cantidad de inyectores de
distinto tamaño requerida para una
operación reduciendo de esta manera los
costes totales.