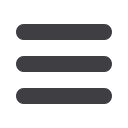

EuroWire – Marzo 2009
145
articolo tecnico
L’azione di un ritardante di fiamma consiste
nell’eliminare o limitare uno dei fattori,
agendo fisicamente o chimicamente (o in
entrambi i modi) sui prodotti liquidi, solidi e
gassosi che si formano durante il processo.
L’azione fisica è di tre tipi:
Raffreddamento del processo di feedback
•
termico, che interrompe la fornitura del
calore necessario a proseguire la pirolisi
del materiale polimerico.
Diluizione della miscela di combustione.
•
Formazione di uno strato protettivo,
•
ove il materiale polimerico solido viene
protetto con l’ossigeno proveniente
dalla consistente fase gassosa mediante
uno strato protettivo solido o gassoso.
Si ha così una riduzione del calore
irradiato al polimero, con conseguente
rallentamento della pirolisi e riduzione
dell’apporto di ossigeno al processo di
combustione.
L’azione chimica si può distinguere in:
Reazione in fase gassosa: i radicali si
•
generano dal ritardante di fiamma
chimicamente per agire sul processo di
combustione.
La reazione in fase condensata può
•
avvenire in due modalità. La prima
consiste nella formazione di uno
strato protettivo di carbonio (residuo
carbonioso) sulla superficie del polimero,
che presenta le caratteristiche di un
isolante termico e funge da barriera
fra i prodotti della pirolisi e l’ossigeno.
La seconda consiste nell’aumento di
questo strato e nel ritardo del processo di
feedback termico.
Il ritardante di fiamma addizionato al
materiale può essere di vari tipi:
Reattivo: reagisce chimicamente con il
•
polimero.
Additivo: miscelato al polimero.
•
Reattivo ed additivo: presente nel
•
materiale in entrambe le forme.
La scelta del ritardante di fiamma è
influenzato dai seguenti fattori:
Tossicità
•
Biodegradabilità
•
Stabilità del calore nel polimero
•
Il triossido di antimonio (Sb
2
O
3
) viene
normalmente addizionato al fine di ridurre
l’infiammabilità
del
PVC
plasticizzato;
tuttavia il triossido di antimonio consente di
arrestare più efficacemente il meccanismo
della catena dei radicali nella fase gassosa,
ma aumenta la quantità di fumo generato
in caso di incendio. Numerose aziende
specializzate nel trattamento del PVC
hanno dimostrato interesse in altri additivi
ritardanti di fiamma che consentono una
riduzione dell’infiammabilità senza produrre
componenti tossici o corrosivi. Il ritardante
di fiamma non dovrebbe influenzare
negativamente le caratteristiche specifiche
del PVC.
Sarebbe inoltre auspicabile che qualsiasi
miglioramento della capacità di resistenza
alla fiamma fosse associato ad una riduzione
della densità dei fumi. In caso di incendio,
il PVC rilascia del cloruro d’idrogeno (HCl),
con l’umidità sempre presente nell’aria.
Normalmente si utilizza il carbonato di
calcio nel PVC come additivo innocuizzante
dell’acido e filler economico. In definitiva,
un ritardante di fiamma ideale dovrebbe
presentare anche questi vantaggi.
3.3 Studio della possibilità di
incorporare i nanofiller nel PVC
Recentemente, i nanocompositi polimerici
(PNC), e in particolare i nanocompositi
polimero/argilla,
hanno
suscitato
un
notevole interesse. Si possono ottenere tre
tipi principali di nanocompositi quando
un silicato stratificato viene disperso in
una matrice polimerica. Ciò dipende dalla
natura dei componenti utilizzati come la
matrice polimerica, il silicato stratificato e il
catione organico. Se il polimero non riesce ad
intercalarsi tra le lamine di silicati, si ottiene
un microcomposito. Tale composito a fasi
separate presenta le stesse proprietà dei
microcompositi tradizionali. Oltre a questa
famiglia classica di compositi filler-polimero,
si possono ottenere
3.3 Studio della possibilità di
incorporare i nanofiller nel PVC
Recentemente, i nanocompositi polimerici
(PNC), e in particolare i nanocompositi
polimero/argilla,
hanno
suscitato
un
notevole interesse. Si possono ottenere tre
tipi principali di nanocompositi quando
un silicato stratificato viene disperso in
una matrice polimerica. Ciò dipende dalla
natura dei componenti utilizzati come la
matrice polimerica, il silicato stratificato e il
catione organico. Se il polimero non riesce ad
intercalarsi tra le lamine di silicati, si ottiene
un microcomposito. Tale composito a fasi
separate presenta le stesse proprietà dei
microcompositi tradizionali.
Oltre a questa famiglia classica di compositi
filler-polimero, si possono ottenere due tipi
di nanocompositi:
Strutture intercalate, che si formano
•
quando una o più catene polimeriche
estese sono intercalate (frapposte)
con strati di silicato. Si ottiene così
una struttura multistrato ben ordinata
formata da strati polimerici alternati con
strati inorganici.
Le reazioni successive di polieni coniugati
altamente reattivi causano la reticolazione
o la scissione della catena polimerica, e
formano benzene e tracce minime di benzene
condensato e/o alcalinizzato secondo la
temperatura e l’ossigeno disponibile (reazioni
secondarie).
La degradazione deve essere controllata
con l’aggiunta di agenti stabilizzatori.
L’agente stabilizzatore di calore deve evitare
la reazione di deidrodeclorinazione che è il
processo primario di degradazione.
I sistemi calcio-zinco rappresentano una
buona alternativa agli agenti stabilizzatori
a base di piombo, come dimostra il recente
aumento del suo utilizzo. Le principali aree
di applicazione in cui i sistemi Ca-Zn sono
maggiormente presenti sono il settore del filo
e del cavo, gli interni delle automobili, seguiti
da tubi e profili.
I composti metallici sono stati selezionati
come stabilizzatori senza piombo perché il
loro effetto sul corpo umano è trascurabile,
e pertanto la probabilità di essere soggetti a
regolamenti e restrizioni in futuro è minima.
Combinando gli stabilizzatori ottenuti da
questi metalli è stata sviluppata una resina
a base di PVC con uno stabilizzatore senza
piombo adatta all’utilizzo in isolamenti e
rivestimenti di fili.
3.2 La funzione dei ritardanti di fiamma
nel PVC
Il processo di combustione può essere
sintetizzato nelle fasi seguenti:
Riscaldamento
•
Decomposizione (pirolisi)
•
Ignizione e combustione
•
Propagazione con feedback termico
•
Il riscaldamento del materiale mediante
sorgenti termiche esterne aumenta la
temperatura del materiale, ad una velocità
che dipende dall’intensità del calore
emesso, dalle caratteristiche di conduttività
termica del materiale, dal calore latente di
fusione e di vaporizzazione e dal calore di
decomposizione.
Al raggiungimento di una temperatura
sufficiente, il materiale inizia a degradarsi
formando delle miscele gassose e liquidi.
Queste miscele si formano ad una
velocità che dipende dall’intensità con
la quale il materiale polimerico viene
riscaldato. La concentrazione dei prodotti
in
decomposizione,
miscelandosi
con
l’aria circostante, aumenta fino a rientrare
nell’intervallo d’infiammabilità. In questa
situazione, la presenza di una sorgente di
calore causa l’ignizione della miscela. Il calore
generato viene parzialmente irradiato al
materiale (feedback termico), in modo da
proseguire con la pirolisi.
Reazioni a catena
(“meccanismo zip”)
HCI
PVC
HCI
Ciclo di combustione del polimero
▲
▲
Sostanze
volatili
ossigeno
Fiamma
Prodotti
Calore
Polimero
Ciclo di
combustione del
polimero
Dispersione
Fase gassosa
Fase
condensata
Residuo carbonioso