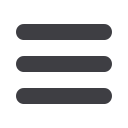

Technical article
May 2015
78
www.read-eurowire.comMeasured and simulated
DC powering of data cables
for power over Ethernet
By Stephen W Simms, Brand-Rex Ltd
Abstract
The increasing demand for higher power
levels in Power over Ethernet (PoE) systems
is evident, with a variety of non-standard
products currently available on the market
which provide power levels in excess of
those stated in IEEE 802.3at.
Higher power levels will allow PoE to be
used in a wider range of applications.
However, they will also increase perfor-
mance risk. With this increase in demand
for more power, and the fact that
installations using PoE technology differ
greatly in terms of their configuration and
environment, it is beneficial to mitigate risk
by using numerical simulation.
The work presented here provides
numerical simulation and experimental
verification of the thermal properties of
data cables under DC powering which is
used in PoE applications.
Introduction
The supply of DC power to end devices
along the same electrical path used
for AC signal communication has been
successfully employed for many years, eg
in telephones and audio equipment.
The technique used to provide this
functionality is commonly known as
‘phantom powering’. In relation to Ethernet,
this technique allows power from the
Power Sourcing Equipment (PSE) to be
delivered to the Powered Device (PD) on
the same pair that is used for data.
The DC power is applied to the centre
tap of the signal coupling transformer
and does not interfere with data transfer.
This allows PoE to be deployed over
1000BASE-T systems, in which data is
carried on all four pairs.
IEEE 802.3at standardisation in 2009 stated
the system parameters required for Type 1
(PoE) and Type 2 (PoE+)
[1]
.
The standard classifies nominal highest DC
current values of 0.35A and 0.60A per pair,
for Type 1 and Type 2, respectively. Some
of the most common applications which
use PoE technology include wireless LAN
access points, VoIP telephones and network
cameras.
Applying electric current to a conductor
releases heat energy, an effect known
as Joule heating. In relation to Ethernet
cables and components, this heating
effect causes concern due to the rise in
attenuation, which has a limiting effect
on link length. This concern is heightened
for cables with a higher resistance than
standard cables, eg copper clad aluminium
(CCA)
[2]
, and smaller diameter (26 AWG)
solid copper conductor cables.
In 2009, IEC subcommittee 46C put
forward a test method (46C/906/NP)
entitled ‘Proposal for measuring of heating
of data cables by current’
[3]
.
In this paper, the aim is to achieve a strong
correlation between simulation and the
proposed measurement method regarding
the DC powering of Ethernet cables for
PoE applications. The paper also aims
to compare temperature rise due to DC
powering of CCA cable with cables which
have solid copper conductors.
Numerical modelling
A 2D model was set up using COMSOL
Multiphysics 4.4, a software package
which utilises the Finite Element method
[4]
.
The model was set up to replicate the
proposed measurement method
[3]
, which
allowed for a comparison between theory
and practice.
In order to achieve this, a five-cable
linear configuration was set up with the
intention of providing a good prediction of
the thermal behaviour at the centre cable
without the need for including additional
cables in a model requiring higher
computational resource.
Heat capacity at constant pressure,
density and thermal conductivity material
properties were applied to represent the
constituent parts of the Cat6A 26 AWG U/
FTP cable. These properties were applied
to the copper (Cu) conductor, aluminium/
PET (Al/PET) tape, Low Smoke Zero
Halogen (LSZH) jacket, and polyolefin
insulation, see
Figure 1
. Conduction,
convection and radiation heat transfer
mechanisms
[5]
were accounted for in the
model.
Simulated electric energy was applied
to one pair of each cable in the model.
A stationary solver was used to determine
the thermal behaviour for (a), a point at the
centre of one of the energised conductors
(see probe position in
Figure 1
) and (b), a
2D temperature plot of the cross-section,
Figure 2
.
Air
Energised
pairs
LSZH
jacket
Probe
Polyolefin
Cu
AI/PET tape
▲
▲
Figure 1
:
Simulation setup in COMSOL Multiphysics