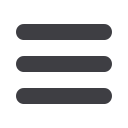

Technical article
May 2015
79
www.read-eurowire.comFrom the 2D plot, and as expected, the
maximum temperature of the arrange-
ment is evident in the proximity of the
energised conductors.
Test method and results
The test method proposed by IEC
Subcommittee 46C
[3]
was followed in
order to establish the rise in conductor
temperature due to DC powering. This
method involved measuring voltage
supplied and jacket temperature using
a 100-metre sample of cable wound
onto a reel and positioned within an
environmental chamber fixed at 20°C, see
Figure 3
. This method was followed using
a sample of Cat6A U/FTP cable with solid
copper 26 AWG conductors, as simulated
in section 2.
The cable sample was conditioned at
20°C for at least 16 hours before testing.
A thermocouple of J type was positioned
along the jacket at the halfway point of
the cable. Using a Keithley 2200-60-2 (60V,
2.5A) bench power supply operating in
constant current mode, a current (I) of 0.6A
was applied to the pair under test with the
far end of the sample short circuited.
Temperature and voltage data was logged
at 15 second intervals using National
Instruments LabVIEW software
[6]
.
The temperature of the cable sample
increased due to the Joule heating effect,
and after a certain time, the temperature
stabilised. At this point in time, the heating
due to the DC power input became equal
to the radiated power of the sample and
the temperature was prevented from
rising further.
Conductor resistance was calculated
based on voltage immediately after the
power was switched on (U
0
), equation (1),
and after the temperature had stabilised
(U
T
), equation (2). Change in (or delta)
conductor temperature (Δt) was then
calculated using initial (R
20
) and stabilised
(R
t
) resistance, equation (3).
This methodology was repeated using
four different current (I) values, ie 1.0A,
1.4A, 1.8A and 2.2A.
Figure 4
shows the
change in conductor temperature versus
DC current level simulated at the probe
(see
Figure 1
) and calculated from the
measurement.
Results show a linear relationship with
both delta conductor temperature and
current plotted on logarithmic scales.
Based on this relationship, it was possible
to apply an approximation, in the format
Δ
t
=
x
*
I
y
, which could be used to predict
conductor temperature rise for current
values outwith the range measured.
For the Cat6A 26 AWG U/FTP cable, this
approximation was found to be:
(INSERT IMAGE/CALCULATION 1 HERE)
Using the approximation, a current of 3A
would provide a temperature rise of 20.7°C
for a single cable within an environment
fixed at 20°C.
The correlation between simulated and
measured results was further investigated
from a statistical point-of-view using
a Paired t-test via Minitab software
[7]
.
Figure 5
shows an individual value plot
of the temperature differences between
simulation and measurement, which also
shows the 95 per cent confidence interval
based on these differences. The results
shows that 95 per cent of additional
simulated and measured values are
expected to fall within the ±0.1 difference
range, confirming excellent correlation. As
such, the null hypothesis of no difference
in mean values between the two sets of
data is not rejected.
Copper clad aluminium
A sample of UTP CCA cable with 24
AWG conductor size was acquired and
measured as per the Cat6A 26 AWG U/
FTP cable sample in section 3. The DC loop
resistance of the pairs under investigation
for each cable type are given in
Table 1
.
For comparison, a Cat5e UTP cable with
24 AWG solid copper conductors was
included in the study.
Due to the high resistance of the CCA
cable under investigation, the high voltage
required to provide a current of 2.2A
was not possible using the bench power
supply.
In other words, as the temperature and
resistance increased, the voltage required
(in order to meet Ohm’s Law) was larger
than the maximum voltage 60V) of the
bench power supply. A current value of
1.95A was chosen in order to generate the
fifth data point.
Figure 6
shows the change in conductor
temperature,
versus
DC
current
level, which was calculated from the
measurement. For the CCA cable sample,
approximated conductor temperature rise
was found to be:
(INSERT IMAGE/CALCULATION 2 HERE)
AWG
DC loop
resistance (Ω)
Cat6A
26
23.3
CCA
24
28.4
Cat5e
24
18.2
Cable sample
Thermo couple
Temperature (ºC)
DC power supply leads
▲
▲
Figure 2
:
Cross-sectional temperature plot
▲
▲
Figure 3
:
Measurement
setup
▲
▲
Table 1
:
DC loop resistance of pair under
investigation for each cable type