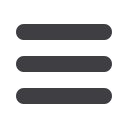

INFORMS Philadelphia – 2015
335
1 - Quality at the Source or Quality at the End? Managing Supplier’s
Quality under Information Asymmetry
Mohammad Nikoofal, Católica Lisbon School of Business &
Economics, UCP, Palma de Cima, Lisbon, 1649-023, Portugal,
mohammad.nikoofal@ucp.ptIn this paper, we first develop and then compare two different mechanisms for
the buyer in order to control quality improvement efforts exerted by the supplier
when the supplier has private information about his inborn reliability.
2 - Optimal Monitoring Decisions for Asset Based Lending
Nikolaos Trichakis, Harvard Business School, Boston, MA,
United States of America, HBS,
ntrichakis@hbs.edu,Dan Iancu,
Do Young Yoon
We consider a firm financing its operations by collateralizing its working assets,
e.g., inventory. To mitigate the risk due to the assets’ uncertain valuation, the
lender has a monitoring option entitling him to early repayment by liquidation.
We derive the optimal liquidation policy, showing that it can have a nonthreshold
structure. We derive bounds on the optimal monitoring time, and leverage them
to devise simple heuristics, which perform well in numerical studies.
3 - Capital Structure with Flexible Future Investments
Qi Wu, Case Western University, Cleveland, OH, United States of
America, Weatherhead School of Management, CWRU,
qxw132@case.edu,Peter Ritchken
We analyze the interaction between investment and financing decisions in a
dynamic contingent claims model where the firm has the ability to dynamically
control production decisions of assets in place and has growth options to invest in
that can be financed with debt and equity. The fundamental question to be
addressed is how investment timing and financing decisions are affected by the
existing capital structure and the nature of the operating flexibility inherent in
the growth options.
4 - Make-to-Order vs. Make-to-Stock when Firms Compete, Input
Costs, and Demand are Stochastic
Danko Turcic, Associate Professor of Operations, Olin Business
School, Washington University in St. Louis, St. Louis, MO, United
States of America,
turcic@wustl.edu, Guang Xiao, Panos Kouvelis
This paper provides a new rationale for why firms choose long and short
production lead times that is based, in part, on non-competitive behavior in
product markets. We identify a set of conditions, which imply that some,
otherwise identical, production firms want to choose long production lead times,
while others choose short production lead times. The conditions are: (i) stochastic
production costs, (ii) price-dependent demand, and (iii) strategic inventory
withholding.
TC49
49-Room 105B, CC
Multi-Echelon Inventory Modeling
Sponsor: Manufacturing & Service Oper Mgmt/Supply Chain
Sponsored Session
Chair: Sean Willems, University of Tennessee, 453 Haslam Business
Building, Knoxville, TN, 37996, United States of America,
willems@bu.edu1 - Velocity-based Storage in a Semi-automated Order
Fulfillment System
Stephen Graves, MIT, 77 Massachusetts Avenue, Cambridge, MA,
02139, United States of America,
sgraves@mit.edu, Rong Yuan
Online retailers continue to invest in technology to improve the efficiency of
order fulfillment. This technology creates new operating challenges and
opportunities. We examine a semi-automated fulfillment system in which pickers
and stowers are stationary, and the inventory storage units are brought to them.
We evaluate the effectiveness of velocity-based storage and consider how to
deploy a velocity-based storage policy in light of picking, stowing and storage
decisions.
2 - Incorporating an Operational Layer into the Guaranteed-service
Inventory Optimization Approach
Steffen Klosterhalfen, University of Richmond, 1 Gateway Road,
Richmond, VA, 23173, United States of America,
steffenklosterhalfen@googlemail.com,Daniel Dittmar
The existing guaranteed-service contributions assume bounded demand and do
not explicitly model how excess demand is handled by some type of flexibility
measure. The lack of a clear operational description leaves the material flow
representation somewhat incomplete and renders the approach controversial. We
incorporate operating flexibility in the form expediting. By doing so we can work
directly with the external (unbounded) demand and the entire material flow is
easy to trace and understand.
3 - Multi-item Spare Parts Inventory Planning with Selective use of
Advance Demand Information
Geert-Jan Van Houtum, Full Professor, Eindhoven University of
Technology, P.O. Box 513, Eindhoven, 5600MB, Netherlands,
g.j.v.houtum@tue.nl, Tarkan Tan, Engin Topan
We propose a multi-item, spare parts inventory system model with a general
representation of imperfect demand information. We determine which parts
should be monitored and how much stock should be kept for each component so
that a given aggregate system availability is maintained. Our model allows excess
inventory on stock and on order to be returned to the central depot or external
supplier at a certain return cost. We also characterize the optimal ordering and
return policy.
TC50
50-Room 106A, CC
Operations Economics
Sponsor: Manufacturing & Service Operations Management
Sponsored Session
Chair: Terry Taylor, U.C. Berkeley, Haas School of Business,
2220 Piedmont Avenue, Berkeley, CA, United States of America,
taylor@haas.berkeley.eduCo-Chair: Wenqiang Xiao, Associate Professor, New York University,
Stern School of Business, 44 West Fourth Street, 8-72, New York, NY,
10012, United States of America,
wxiao@stern.nyu.edu1 - Strategic Outscouring under Competition and
Asymmetric Information
Lusheng Shao, University of Melbourne, Melbourne, Australia,
lusheng.shao@unimelb.edu.au,Xiaole Wu, Fuqiang Zhang
This paper studies two firms’ outsourcing strategies under competition and
asymmetric cost information. We find that without asymmetric information, the
firms will choose the supplier with smaller cost uncertainty. However, with
information asymmetry, the supplier with greater cost uncertainty may be
preferred.
2 - Information Preferences in the Supply Chain under
Strategic Inventory
Abhishek Roy, PhD Student, McCombs School of Business,
University of Texas at Austin, 2110 Speedway Stop B6500,
Austin, TX, 78712, United States of America,
abhishek.roy@utexas.edu, Steve Gilbert, Guoming Lai
We investigate how the possibility of strategic inventory influences the
preferences for information sharing between supply chain partners. Among other
results, we show that the presence of strategic inventory may alter traditional
information preferences of the supply chain partners regarding the creation of a
mechanism for sharing information about the retailer’s operation with the
supplier.
3 - Product Quality in a Distribution Channel with Inventory Risk
Kinshuk Jerath, Columbia University, 521 Uris Hall, 3022
Broadway, New York, NY, 10027, United States of America,
jerath@columbia.edu, Sang Kim, Robert Swinney
We analyze a situation in which a product has to be designed and sold under
demand uncertainty. We consider the jointly optimal quality and inventory
decision in both a centralized channel (a single firm determines both) and a
decentralized channel (a manufacturer determines quality while a retailer
determines inventory), and discuss how demand uncertainty impacts the optimal
quality-inventory pair and how coordination of the decentralized channel may be
achieved.
4 - Congested Platforms
Terry Taylor, U.C. Berkeley, Haas School of Business,
2220 Piedmont Avenue, Berkeley, CA, United States of America,
taylor@haas.berkeley.eduIn a platform business model, the platform firm provides a per-service wage
payment to independent agents (e.g., drivers in riding-sharing services (e.g.,
Uber), shoppers in delivery services (e.g., Instacart)) to motivate them to provide
service to customers. This paper using a queueing model to examine the impact of
congestion on the platform’s optimal price and wage.
TC50