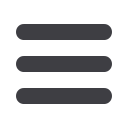

Rocklinizer Metal Impregnator在金属表面沉积和浸渍耐磨电极材料用来预防磨损和维护。它提供完整的动力
装置、电极腹包和使用手册。
有三种类型的电极可以与Rocklinizer一起使用:碳化钨电极适用于高速钢材和其他金属表面,用于延长使用
寿命和减少磨损;钛碳电极表面密封碳化物来防止碎片,“硬岩石”电极材料适用于通过重建公差加强、改
造尺寸过小的工具,用于维护和提供抓取面。
沉积可用于0.0002” 到0.007” 的单一应用中,通过机器设置可控制在0.0001”内。这是一个比先前任何
一个型号重的最大的沉积。Rocklin表示使用Rocklinizer表面处理可以增加生产率,降低易腐蚀切削工具、模
具机配件的成本。
Rocklin Manufacturing Co – USA
Fax: +1 712 252 5619
Email:
info@rocklinmanufacturingco.comWebsite:
www.rocklinmanufacturingco.com- - - - - - - - - - - - - -
New stand with quick re-tooling
OTO Mills SpA, Italy, has expanded its production range, with the addition of a new stand that introduces
some innovative concepts that can also be exported on other line dimensions.
The new stand, model OTO 40616, which features a quick re-tooling system, involves the assembly and ad-
justment of four rollers, of which two are driving rollers with horizontal axle, and two are idle with vertical axle.
The maximum diameter of tube that can be produced will be 406mm (16”) and squares and rectangular by-
products with maximum thickness of 16mm. The stand and driving line have been sized with particular atten-
tion to the ruggedness of the whole assembly, in relation to the range of diameters and thicknesses produced,
as well as the reliability that a system of this size requires.
The re-tooling concept is devised to minimise production changeover times and manual operator interven-
tion, with automated re-tooling and adjustment operations, focusing on simplicity. Re-tooling and the working
position set-up of the new tools are completely automatic.
All adjustments of the roller positions are servo assisted and can be reproduced automatically when the
same production lot reoccurs. These positions can also be easily modified and saved by the operator from
the console.
The quick changeover concept is based on the ability to extract and replace the roller unit on the relevant
mandrels and supports set in one single kit that can be moved to extract from the top. Disengagement of the
Cardan shaft completely frees the mandrels, which can consequently be removed with relevant mountings
and side boxes.
The ability of removing from the top is possible due to the fact that the stands can be opened at the top part
with automatic cycle to let the roller support kit through after slinging it appropriately and hooking it to the
gantry crane, controlled by the operator.
The motorised axles are connected to the reduction gear by Cardan joints and couplings, and using a sliding
coupling system they engage and disengage with the help of a pair of ‘grippers’, driven automatically.
The roller positioning cycle for extraction is performed automatically, so that all the operator has to do is hook
the upper supports and extract the kit in one operation. After the kit in use has been extracted, the operator
may hook the new set of rollers to put it in the stand, again all in one operation.
The standard machine is supplied with a double series of horizontal motorised mandrels and relevant bearing
supports, and double series of side idle roller holder boxes, so that there is always one kit working and one
offline ready for roller changeover.
Additional roller holder kits can be ordered, providing the possibility of leaving them equipped with the same
rollers, and saving re-tooling time offline. A hydraulic device will be supplied offline to make it easier to disas-
semble and assemble the rollers on the motorized axles.
For servo adjustments, each stand with four rollers will be served by four motors and corresponding absolute