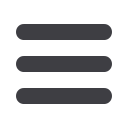

EuroWire – Maggio 2012
93
Articolo tecnico
Quindi è stata valutata la presenza di
segregazione di carbonio nelle barre
laminate a caldo e sono state selezionate
solamente quelle che presentavano un
contenuto di carbonio di 0,78 ± 0,01 di
percentuale in peso per la successiva
trafilatura di filo.
La trafilatura di filo è stata eseguita presso il
Bekaert Technology Centre applicando una
riduzione a 2,5mm di diametro in otto passi
di trafilatura.
Successivamente
è
stato
effettuato
il patentamento in bagni salini con
riscaldamento a 980ºC e quindi a 520ºC.
Il filo patentato è stato poi ulteriormente
trafilato fino a 1mm.
È stata effettuata una prova di trazione in
una macchina elettromeccanica ad una
velocità costante di deformazione di 5,6
10
-4
/s, con un estensimetro di 5cm al 50%.
Sono stati testati due campioni in
ciascuna condizione. Le deformazioni
uniformi sono state definite come
deformazione tecnica al carico di picco
utilizzato per i calcoli della resistenza
massima alla trazione (
UTS
-
Ultimate
Tensile Strength
), e le deformazioni totali
a rottura sono state ottenute dalla lettura
del valore dell’estensimetro al momento
della rottura finale. Tutti i campioni si sono
rotti all’interno della lunghezza specifica
dell’estensimetro,
salvo
diversamente
specificato.
La caratterizzazione microstrutturale è
stata realizzata con microscopia ottica
luminosa in campioni incisi con Picral al
4% e mediante microscopia elettronica
in trasmissione (TEM) su uno strumento
Philips CM120 funzionante a 120kV.
Delle lamine sottili sono state sottoposte
a elettropulitura con un pulitore a doppio
getto Fischione a 32V a temperatura
ambiente, utilizzando una miscela di acido
acetico al 95% e acido perclorico al 5%.
La prova di dilatazione è stata realizzata su
un sistema Gleeble
®
1500. I campioni sono
stati riscaldati a 950°C ad una velocità di
riscaldamento costante di 20°C/s e sono
stati mantenuti isotermici per cinque
minuti. Quindi, l’acciaio è stato raffreddato
in gas elio a velocità di raffreddamento
costanti programmate rispettivamente di
50, 30, 25, 12, 5, 10, 7, 5, 5, 2, 5 e 1°C/s.
Sono
state
realizzate
delle
prove
consecutive in un campione singolo per
ciascuna lega. La dilatazione del campione
è stata monitorata tenendo conto della
temperatura e del tempo.
Risultati e discussione
Le micrografie ottiche luminose effettuate
a metà della sezione trasversale delle
barre laminate a caldo sono illustrate nella
Tabella 1
.
Sono apprezzabili microstrutture perlitiche.
Non sono state osservate reti di costituenti
proeutettoidi.
▼
▼
Figura 1
:
Micrografie ottiche luminose di barre laminate a caldo in acciaio di base, al boro e ad alto contenuto di
boro. Campioni prelevati trasversalmente rispetto alla direzione di laminazione, nel centro della sezione trasversale,
incisione 4% Picral
▲
▲
Figura 2
:
Micrografo elettronico in trasmissione del
materiale ad alto contenuto di B, laminato a caldo e
raffreddato
Base
B
Alto con-
tenuto
di B
Inizialmente, le barre sono state ridotte da
12,7 a 9,5cm, ottenendo barre quadrate
con angoli arrotondati (
RCS - Round Corner
Square
) e successivamente raffreddate con
aria fino a temperatura ambiente, riscaldate
e laminate fino a 4,76cm.
Quindi il materiale è stato lavorato a
macchina per eliminare gli ossidi e tagliato
in 6-7 blocchi.
La riduzione finale è stata realizzata
in un secondo laminatoio a caldo fino
a raggiungere la dimensione finale di
7,1mm. Dopo la laminazione a caldo, il
materiale è stato raffreddato con aria
fino a temperatura ambiente.
Quindi il materiale è stato tagliato con
una sega in pezzi da 3,7m, prima di essere
trafilato. Sono state ottenute ventiquattro
sezioni di ciascuna lega. Sebbene in
base ai calcoli termodinamici mediante il
programma Thermo‑Calc
®
fosse prevista
una potenziale fragilità a caldo dell’acciaio
ad alto tenore di B, non sono state osservate
rotture o difetti superficiali significativi.
Essendo stata osservata una significativa
decarburizzazione
8
, il materiale è stato
molato senza centri fino ad un diametro
di 5,5mm.